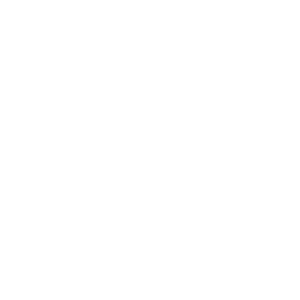
1. Backflow
Problem: The primary function of a check valve is to prevent backflow. However, in some cases, the valve may fail to fully close, allowing fluid to flow in the reverse direction, which is detrimental to system performance.
Causes
- Improper sealing: The valve disc or ball may fail to create a proper seal, especially if debris or corrosion has damaged the sealing surfaces.
- Wear and tear: Over time, the internal components of the valve, such as the seat or disc, can wear down, leading to leaks.
- Incorrect installation: If the valve is installed incorrectly (e.g., upside down or in the wrong direction), it may fail to close properly.
Solution
- Inspect the valve for debris or corrosion on the sealing surfaces and clean or replace the damaged components.
- Ensure the valve is installed correctly, following manufacturer instructions regarding orientation and positioning.
- Regular maintenance and monitoring of check valves will help prevent issues with backflow over time.
2. Valve Sticking or Binding
Problem: A check valve may become stuck or bound, preventing it from opening or closing as it should. This can result in insufficient flow or no flow at all.
Causes
- Debris accumulation: Foreign particles or debris can accumulate inside the valve, causing the disc or ball to stick or become misaligned.
- Corrosion: In corrosive environments, internal components may degrade or seize up.
- High-viscosity fluids: Thick fluids can cause resistance to movement, preventing the valve from operating smoothly.
Solution
- Periodically clean the valve to remove debris or contaminants.
- Consider installing a strainer or filter upstream of the check valve to reduce the likelihood of debris entering the valve.
- Use check valves made from corrosion-resistant materials for applications with corrosive fluids.
3. Chattering or Vibrations
Problem: A check valve may create unwanted noise or vibrations, known as "chattering," when it rapidly opens and closes. This can cause stress on the valve, other system components, and result in inefficient operation.
Causes
- Excessive flow velocity: High flow rates or sudden pressure changes can cause the valve to oscillate between open and closed positions.
- Improper sizing: A valve that is too small for the system may struggle to keep up with the required flow, resulting in instability.
- Valve design: Some check valves, such as swing check valves, are more susceptible to chattering under certain conditions.
Solution
- Install a check valve that is appropriately sized for the system's flow and pressure conditions.
- Consider using silent check valves or tilting disc check valves designed to minimize chattering.
- Use a throttling valve or pressure relief valve upstream of the check valve to reduce pressure fluctuations and stabilize flow.
4. Leakage at Valve Seat
Problem: Leakage can occur at the seat of the valve, allowing fluid to bypass the valve even when it’s supposed to be fully closed.
Causes
- Seat damage: Over time, the valve seat can become worn or damaged, reducing the valve's ability to create a tight seal.
- Improper materials: The valve materials may not be compatible with the fluid type, leading to degradation or erosion of the seat.
- Incorrect installation: The valve seat may not align properly with the valve body, leading to an imperfect seal.
Solution
- Inspect and replace the valve seat when it shows signs of wear or damage.
- Ensure that the valve materials are compatible with the fluid type and consider using more durable materials for high-wear applications.
- Install the valve according to manufacturer guidelines to ensure proper alignment and seating.
5. Pressure Drop Across the Valve
Problem: A significant pressure drop can occur across the check valve, which may reduce the overall efficiency of the system and cause flow restrictions.
Causes
- Improper valve selection: If the check valve is too small for the required flow rate, it can create unnecessary resistance.
- Obstructions: Debris or sediment can accumulate inside the valve, restricting flow and causing pressure loss.
- Design limitations: Some check valves may not be designed to handle high-flow or high-pressure systems, leading to pressure drop issues.
Solution
- Ensure the valve size and design are appropriate for your system's flow and pressure requirements.
- Regularly clean and inspect the valve to prevent obstructions and sediment buildup.
- Consider using a tilting disc check valve or another design that minimizes pressure loss while maintaining effective flow control.
6. Improper Function Due to Vibration or Water Hammer
Problem: In systems with rapid flow changes, the valve may experience issues like water hammer or excessive vibration, which can damage the valve or cause it to malfunction.
Causes
- Rapid valve closure: If the valve closes too quickly, it can create a shockwave in the system (water hammer), leading to sudden pressure spikes that may damage the valve or other components.
- Improper installation: Check valves installed in systems with frequent flow reversals or pressure surges are more likely to malfunction.
Solution
- Install check valves with slower closing mechanisms or use a vacuum breaker valve to control water hammer.
- Implement surge protection devices or pressure relief valves in areas where rapid pressure changes are expected.
- Consider using a spring-loaded check valve or ball check valve for systems prone to water hammer or vibrations.